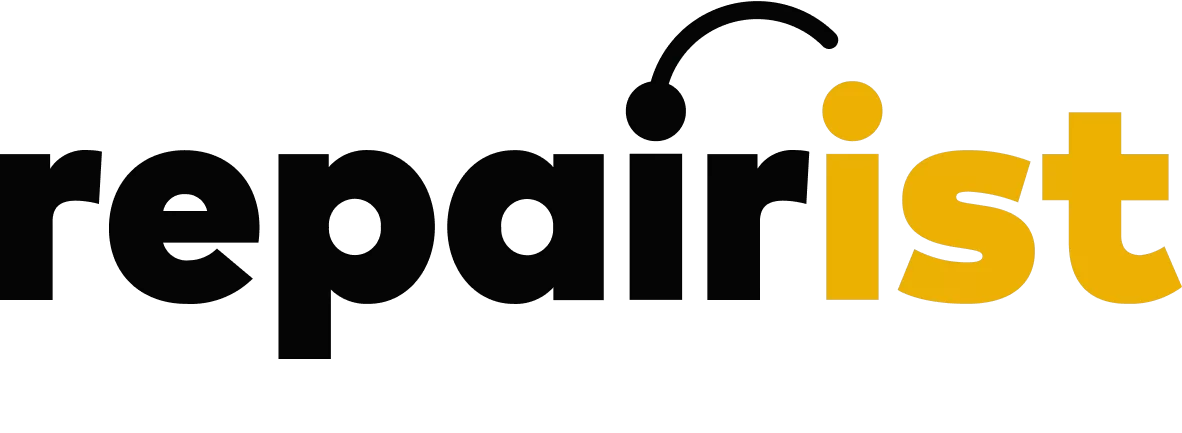
The Advanced Maintenance Management System helps you effectively manage your business’ assets and equipment in the field. Accessible from anywhere at any time, it enables your field teams to plan, track and document their tasks faster and more efficiently. With the Mobile Maintenance Management System, you can optimize your maintenance processes, reduce your operating costs and extend the lifespan of your equipment.
- Mobile Maintenance Management System
- Enterprise Asset Management
- Manageable Work Orders
- Spare Parts and Inventory Management
- Planned and Preventive Maintenance
- CMMS
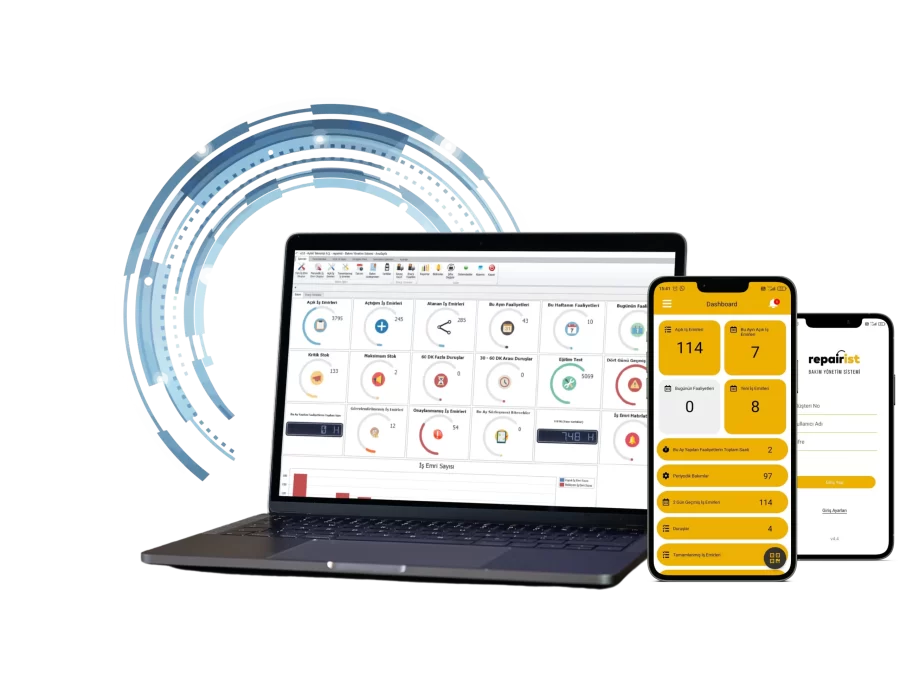
Manage Your Work Orders
Professionally
Tired of paper and lost work orders? With a centralized Maintenance Management System you can organize your work orders, planned and preventive maintenance.
Advanced Asset Maintenance Management System
When emails, phone calls and notepads cause chaos and you need a system that’s easy for your maintenance team to use, try Repairist.
Don't Forget
Work Order
Notifications
Once submitted, job requests are automatically synchronized between your computer, mobile phone and tablet so that your data is up-to-date and accessible on every device.
Smart Mobile Asset and Work Management System
It allows anyone you authorize to send work requests to your maintenance department by simply scanning a QR code (barcode) via mobile devices.
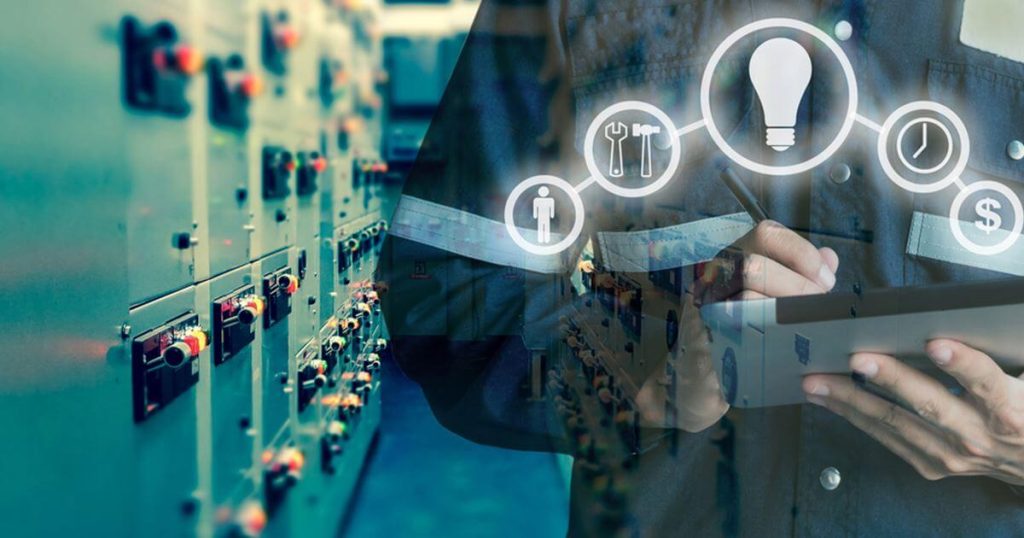
World Class Institutional Asset Management
Are you tired of trying to organize the clutter of your equipment, wondering if the equipment has been properly repaired, not knowing the cost of maintenance and all the other problems that come with managing assets? Manage thousands of assets easily from anywhere with Repairist Maintenance Management System and Enterprise Asset Management module. You can easily search and monitor assets in a tree structure.
- Know the current operational status of your assets and their costs to you.
- Keep complete and detailed maintenance notes.
- Organize your assets and their sub-assets in the desired hierarchy.
- MTTR, MTBF etc. View real-time and detailed reports with KPIs.
- Find information quickly and easily with QR Codes (barcodes).
- Get real-time asset data with a sensor connection (Requires integration).
Your Data on Your Side with Customized Indicators
Let’s face it, the first step to improve your operations is knowing the good and the bad. With Repairist’s Dashboards, you can finally start to find the things that went wrong, if any, and put data-backed plans into action. This results in reduced labor/repair costs, shorter breakdown periods, and more. With Repairist’s Custom Dashboards;
- Be aware of where and why your maintenance budget is spent.
- Find out which asset costs the most and why.
- Create your own customized KPIs.
- View automatically generated and updated reports based on your metrics.
- Easily view shared reports with Repairist.
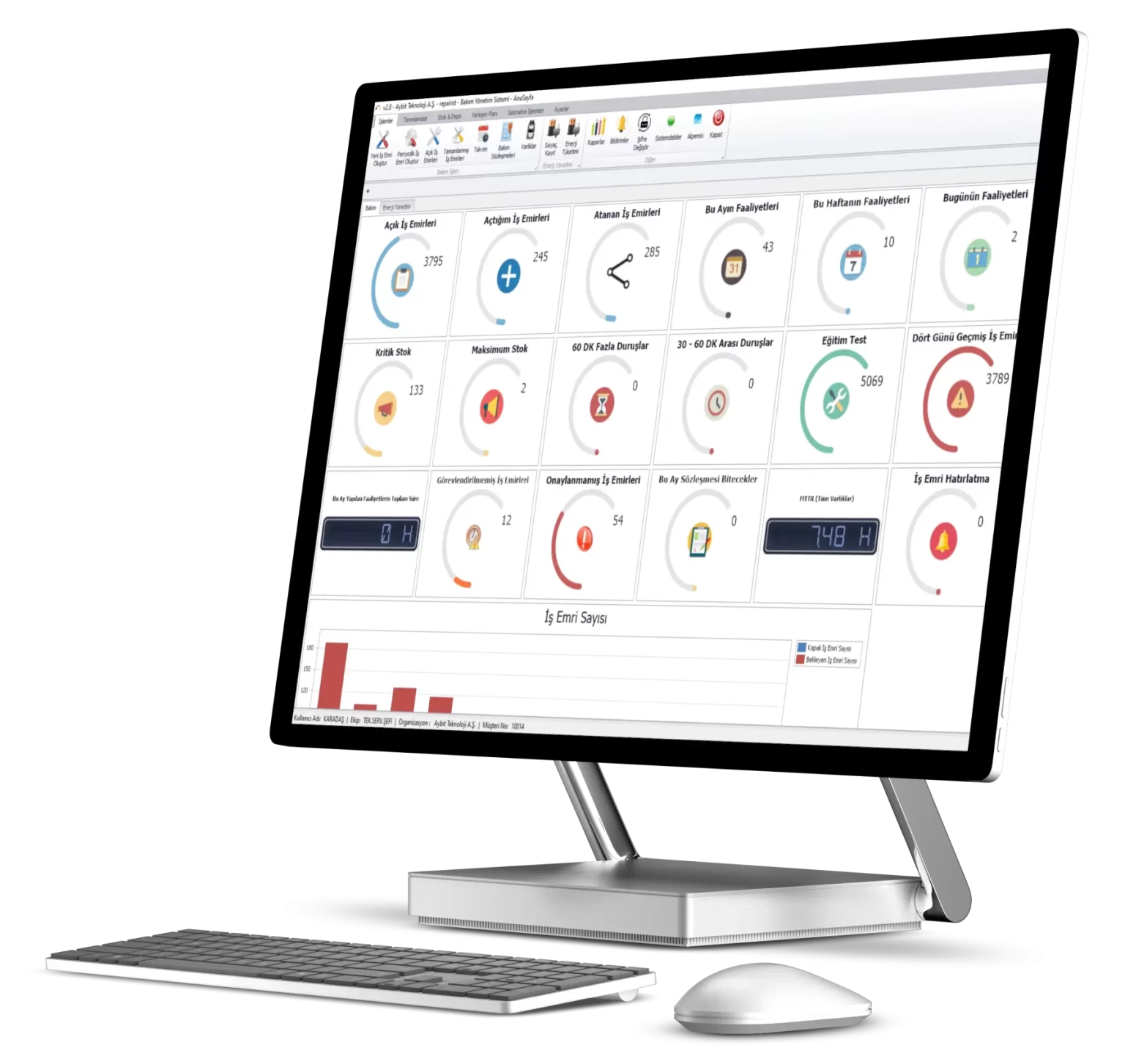
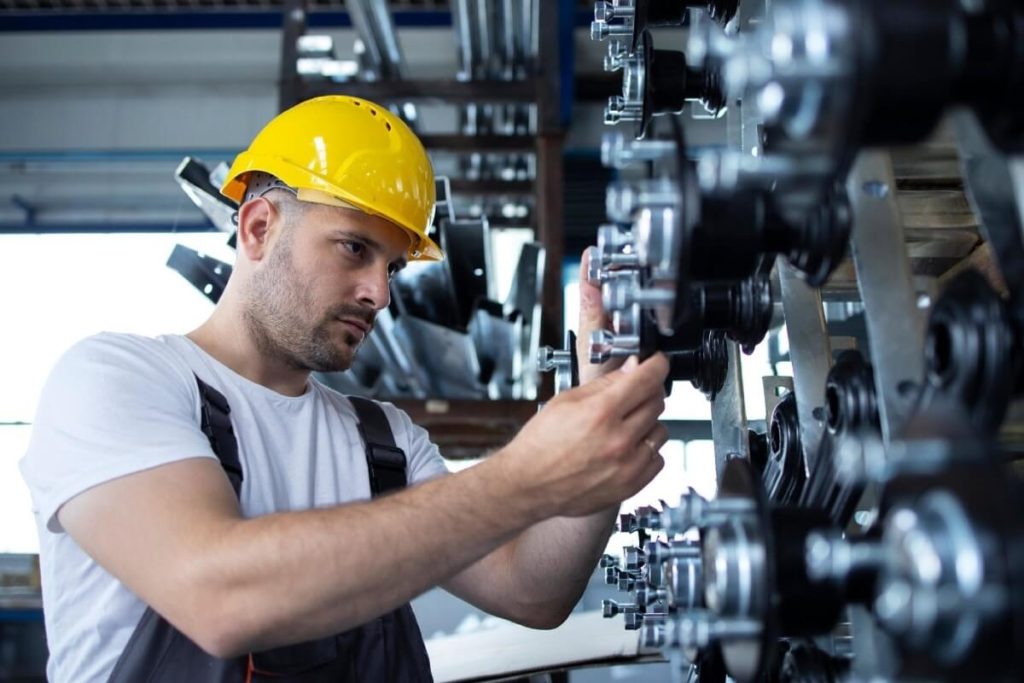
Create Detailed and Powerful Preventive Care
Repairist creates simple and intuitive PM plans and guides your technicians to make sure your work is done correctly. It allows you to create simple checklists or conditional logic. It enables you to create and document information such as how to perform maintenance and which parts to replace so that even new staff know exactly what to do without the need of additional training. By using Repairist’s PM Plans generator you can;
- Ensure to check that a task has been completed.
- Automate meter readings.
- Attach images or review reports.
- Select from predefined drop-down lists.
- Initiate work orders under certain conditions.
- Provide instructional text and visuals. For example, lubricate this particular gear.
- Set estimated times to be completed.
- Identify spare parts to be used.
- Set default operating priorities (Urgent, Medium, Low, etc.).